Mechanical Catalog
Vacuum casting
Our vacuum casting process is designed to replicate intricate and complex parts with remarkable accuracy. Whether you require functional prototypes or small production runs, we have the expertise and technology to bring your designs to life. We prioritize quality at every step of the casting process. Our meticulous attention to detail and rigorous quality control measures ensure that each cast…
Description
Sizes and weight
How to use
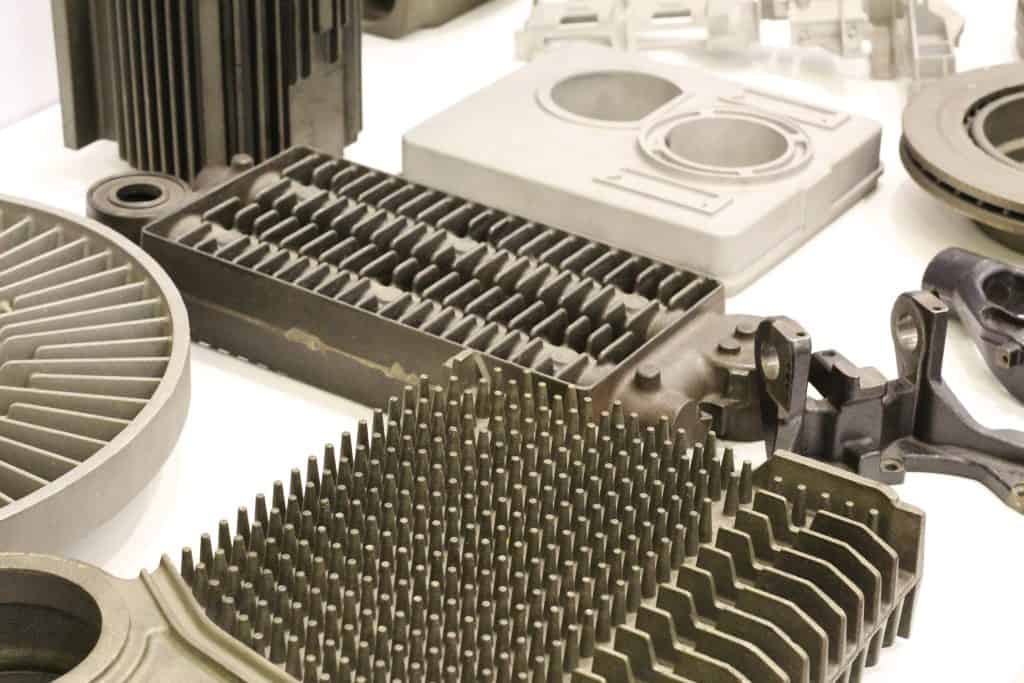
More from the Mechanical Catalog
Magnets
View ProductFinishing
View Product3D printing
View ProductSheet Metal Fabrication
View Product